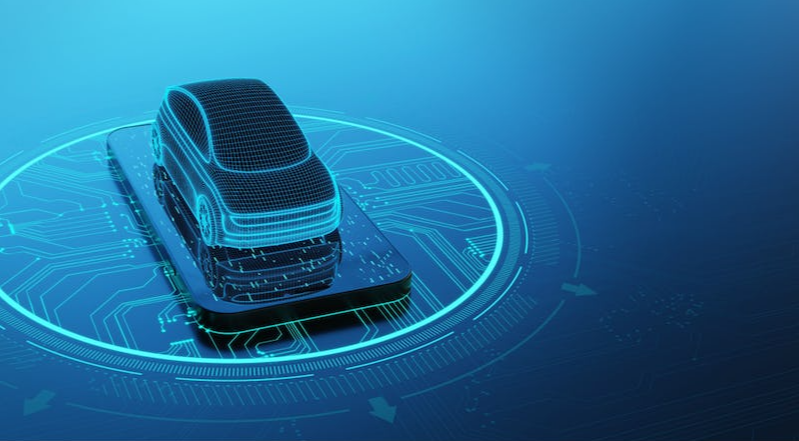
마이크로컨트롤러(컨트롤러, MCU 등 다양한 이름으로도 불림)는 현대 자동차를 구성하는 중추적인 부품입니다. 자동차의 동력이 가솔린, 디젤, 전기, 수소, PDG 등 어떤 것이든 상관없이 자동차의 기능은 컨트롤러에 크게 좌우됩니다. 이러한 컨트롤러의 공급이 부족할 경우 자동차 산업이 무릎을 꿇을 수 있다는 사실도 확인되었습니다.
IDTechEx의 보고서인 "자율주행 및 전기차용 반도체 2023-2033"에 따르면 현재 자동차 컨트롤러 분야에서 더 많은 연산 능력과 새로운 차량 아키텍처 옵션을 제공하기 위해 많은 움직임이 일어나고 있는 것으로 나타났습니다. 컨트롤러로 이러한 트렌드를 거스르고 있는 기업 중 한 곳이 바로 Tesla입니다.
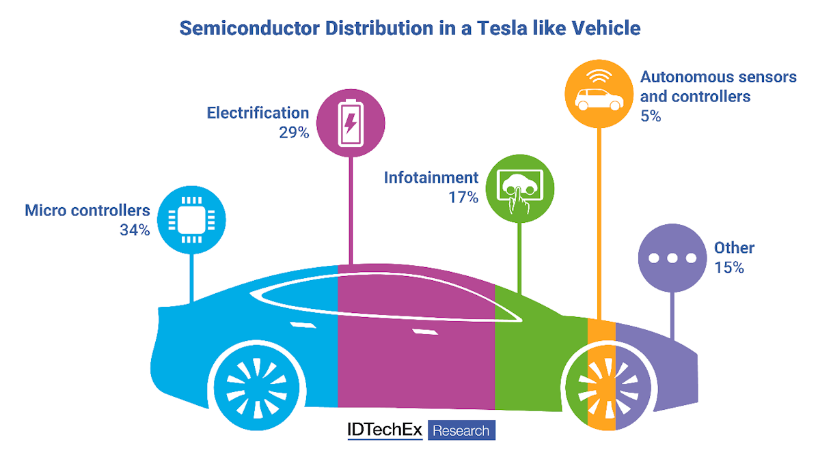
Tesla는 Model S부터 컨트롤러를 설계하기 시작했지만, Model S의 컨트롤러 중 20%만 사내에서 설계되었습니다. 이 비율은 수년에 걸쳐 증가하여 Model Y는 자체 설계 컨트롤러가 61%, 사이버트럭은 85%까지 올라갔습니다.
Tesla는 2023년 투자자의 날 프레젠테이션에서 차세대 차량에는 100% 자체 설계된 컨트롤러가 탑재될 것이라고 발표했습니다. 컨트롤러 설계를 완전히 자체 개발하는 것의 장점 중 하나는 Tesla가 와이어링 하네스 설계에 대한 완전한 자율성을 확보할 수 있다는 것입니다. 이것이 생각보다 더 큰 이유입니다.
Tesla는 와이어링 하네스 감소 분야에서 업계를 선도하고 있습니다. 요즘 자동차에 탑재되는 전자장치의 양이 많아지면서 모든 부품이 서로 통신할 수 있도록 거의 무한대에 가까운 미로와 같은 배선이 있는 것은 당연한 일입니다. 그러나 큰 와이어링 하니스는 여러 가지 문제를 야기하는데, 우선 무게가 가장 큰 문제입니다.
자동차의 길이가 몇 미터에 불과하더라도 여러 배선을 수백 번 연결해야 한다면 그 무게는 금세 늘어나게 되고, 최근의 차량에는 말 그대로 총길이가 수 마일에 달하는 하네스가 장착되기도 합니다. 5마일의 절연 구리 케이블은 무겁습니다. IDTechEx의 연구에 따르면 와이어링 하니스의 무게는 60kg이 넘을 수 있으므로 테슬라가 무게를 17kg이나 줄인 것은 인상적인 결과입니다.
대형 와이어링 하니스가 바람직하지 않은 또 다른 이유는 제작에 소요되는 인건비 때문입니다. 단일 와이어링 하네스에는 수백, 때로는 수천 개의 단자가 있습니다. 각각의 와이어를 자르고, 벗기고, 압착하고, 커넥터의 올바른 핀에 끼워야 하는데, 이 모든 작업을 수작업으로 수행해야 합니다.
이러한 작업은 고도의 손재주, 세심한 주의력, 경험, 기술이 필요한 까다로운 작업이므로 기계로 쉽게 복제할 수 있는 작업은 아닙니다.
컨트롤러 설계를 자체 기술로 도입함으로써 Tesla는 중앙 집중식 제어 아키텍처에서 로컬화된 아키텍처로 전환할 수 있었습니다. 중앙 집중식 아키텍처에서는 컨트롤러 하나 또는 소규모 컨트롤러 그룹이 차량 주변의 모든 장치와 통신해야 합니다.
예를 들어 차량의 반대편 끝에 5개의 디바이스 그룹이 있고 4m의 케이블이 필요하다고 가정해 보겠습니다. 예를 들어 각 장치에는 전원용 1개, 접지용 1개, CAN용 2개 등 최소 4개의 연결부가 있다고 가정해 보겠습니다. 따라서 이제 하나의 소규모 장치 그룹을 위해 20개의 전선과 80m의 케이블이 필요합니다.
로컬라이즈 된 아키텍처는 더 작은 컨트롤러가 이러한 디바이스들 사이에서 허브 역할을 한다는 것을 의미합니다. 차량의 중앙 컨트롤러에는 하나의 이더넷 연결이 있고 개별 디바이스에는 아주 작은 연결만 있습니다. 따라서 예를 들어 80m의 케이블을 40m로 줄일 수 있습니다.
컨트롤러 아키텍처를 변경하는 것 외에도 Tesla는 저전압 장치용 48V 아키텍처로 전환하여 더 많은 이점을 제공하고 있습니다. 48V 시스템 또는 저전압 시스템은 센서, 조명, 인포테인먼트 등 드라이브 트레인을 제외한 거의 모든 전자 부품에 전원을 공급하는 데 사용됩니다.
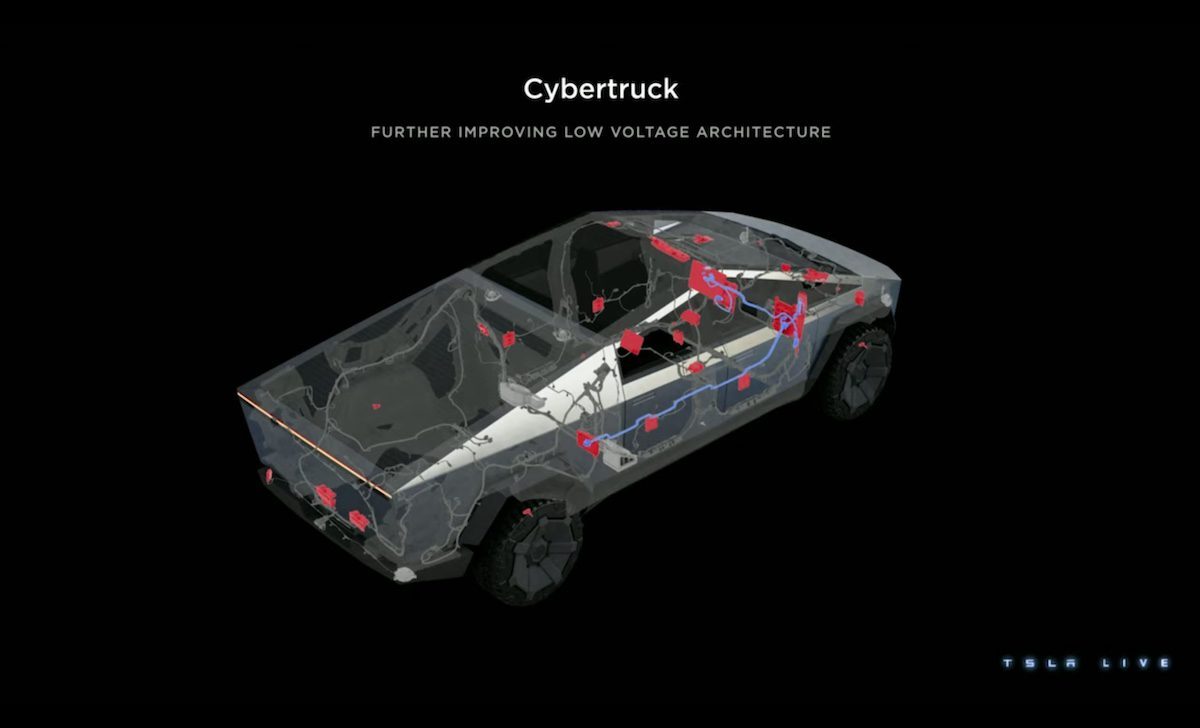
대부분의 차량은 보닛 아래에 있는 납산 배터리에서 전원을 공급받는 12V 시스템을 사용하는데, 이는 150년이 넘은 기술입니다. Tesla에 따르면, 차량 주변의 모든 보조 부하를 포함한 12V 시스템은 최신 차량에서 200 암페어 이상을 공급할 수 있어야 합니다.
그러나 전력은 전압에 전류를 곱한 값이므로 한쪽이 4배가 되면 다른 한쪽은 4분의 1로 줄어들 수 있습니다. 즉, Tesla의 48V 시스템은 차량 주변에 해당 전류의 4분의 1만 필요하므로 훨씬 더 얇은 케이블을 사용할 수 있습니다.
Tesla는 차량 설계 및 생산의 모든 측면을 끊임없이 최적화하는 것으로 명성을 쌓아왔습니다. IDTechEx는 완전히 내부에서 설계된 컨트롤러로의 전환과 48V 저전압 시스템의 채택이 Tesla의 차량 최적화 분야에서 더욱 인상적인 성과를 거두는 시작이 될 것이라고 생각합니다.
차량 전체에 걸쳐 컨트롤러를 완벽하게 제어할 수 있게 됨에 따라 Tesla는 아키텍처를 개선할 수 있는 더 많은 자유를 얻었을 뿐만 아니라 공급망에 대한 협상력도 강화할 수 있게 되었습니다. 자동차 업계는 코로나19 팬데믹 기간 동안 반도체 공급에 대한 민감성을 뼈저리게 깨달았습니다.
차량 컨트롤러가 공급되지 않아 많은 생산 라인이 멈춰 섰습니다. 컨트롤러 설계를 자체적으로 수행함으로써 Tesla는 이러한 장애에 덜 민감해졌으며, 칩을 신속하게 재설계하여 공급을 개선하거나 다른 반도체 파운드리에서 생산 능력을 확보하여 흐름을 이어갈 수 있었습니다.
지난 몇 년 동안 다른 OEM 업체들도 일부 반도체 칩 설계를 자체적으로 수행한다는 소식이 들려왔지만, Tesla는 100% 자체 설계로 기준을 높임으로써 선구자 역할을 하고 있습니다.
Tesla는 이전에 하드웨어 버전 2.5(HW2.5)에서 HW3로 전환할 때 이러한 강점을 입증한 바 있습니다. HW2.5의 중앙 자율주행 두뇌에는 2개의 엔비디아 파커 SoC(시스템 온 칩), 1개의 엔비디아 파스칼 GPU(그래픽 처리 장치), 1개의 인피니언 MCU(마이크로컨트롤러 유닛)로 구성된 4개의 칩이 탑재되었습니다.
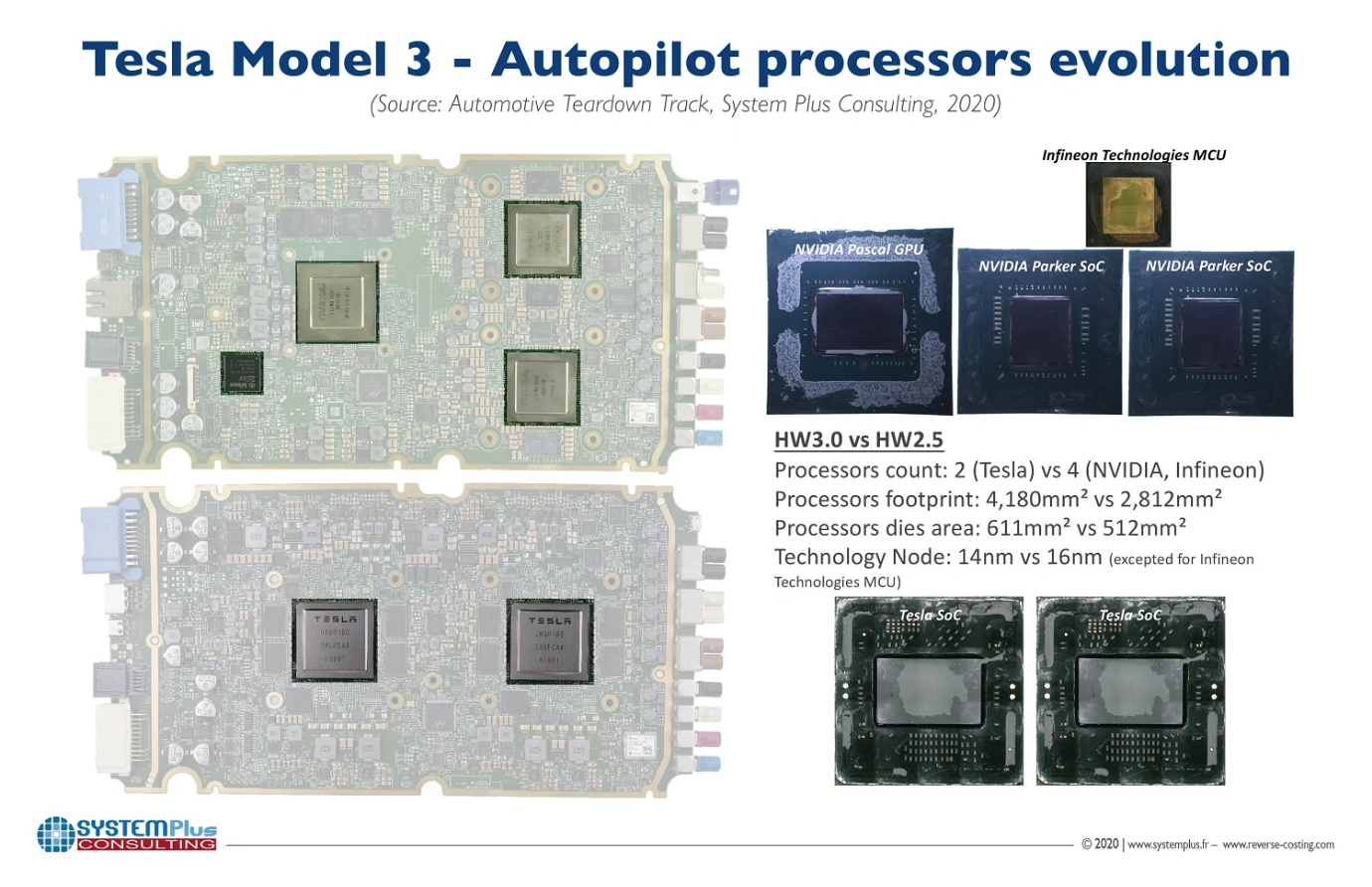
반면, HW 3에는 두 개의 칩만 탑재되었는데, 두 칩 모두 14nm 공정을 사용하여 삼성에서 제조한 Tesla SoC였습니다. TSMC와 글로벌파운드리도 14nm 공정을 보유하고 있어 더 많은 옵션과 잠재적 공급이 가능하기 때문에 Tesla는 더 많은 협상력을 갖게 되었습니다.
또한 엔비디아는 팹리스이기 때문에 칩을 설계한 다음 테슬라와 같이 대형 파운드리에서 생산해야 하므로 공급망이 단축되어 테슬라의 비용 절감으로 이어질 가능성이 높습니다.
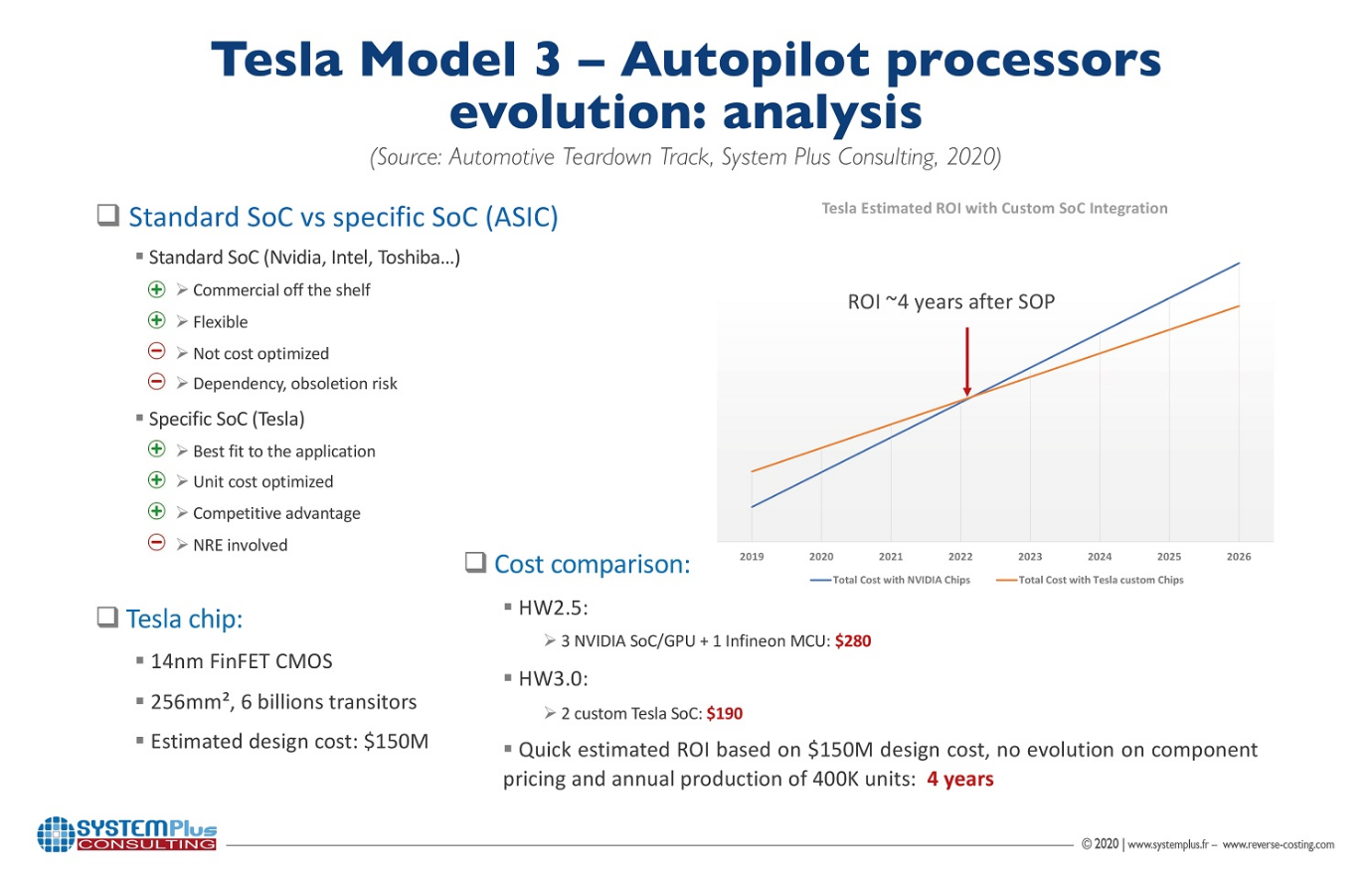
또한 Tesla는 더 많은 설계를 자체적으로 수행함으로써 2차 공급업체가 제공하는 것 이상의 기능을 지정할 수 있다고 말합니다. OEM이 상용 부품을 구매하면 당연히 타협이 따를 수밖에 없습니다.
티어 2의 칩 아키텍처는 가능한 한 시장성이 높고 많은 사람들의 요구를 충족하도록 고안됩니다. 이는 일반적으로 개인의 요구에 맞춰져 있지 않다는 것을 의미합니다. 설계 프로세스를 사내로 가져오는 것은 쉬운 일이 아니지만, 이제 Tesla는 Tesla만을 위해 설계된 칩을 만들 수 있습니다.
IDTechEx의 "자율주행 및 전기차용 반도체 2023-2033" 보고서에서는 기존 반도체 공급망에 대해 자세히 설명하고, 어떤 다른 OEM이 자체 컨트롤러 설계를 검토하고 있으며 그 이유를 설명합니다.
이 보고서는 마이크로컨트롤러에 초점을 맞추고 있지만, "자율주행 및 전기차용 반도체 2023-2033" 보고서는 ADAS, 자율성, LiDAR, 레이더, 카메라, 4G 연결, 5G 연결, 전기 파워트레인, MCU, SOC 등 자동차 전반에 걸친 반도체를 총체적이고 포괄적으로 다루고 있습니다.
'Finance Investment > 자동차와 자동차부품' 카테고리의 다른 글
240116_23년 중국 자동차 어디로 많이 팔렸을까? (0) | 2024.01.17 |
---|---|
230911_리튬 가격 급락세와 보조금 감소한국 양극재업체들 주가에 부담 (0) | 2023.09.12 |
220715_BEV침투율 상승 Tipping point 5% (0) | 2022.07.17 |
210824_라이다 자율주행의 회색빛 전망: 높은 설치비용, 정밀지도 구축의 어려움으로 인한 확장성의 제한 (0) | 2021.08.24 |
2021년 3월 현대차그룹 글로벌 도매 판매, 리테일 판매, 출하량 데이타 (0) | 2021.04.05 |